How Preventive Maintenance Reduces Asset Risks
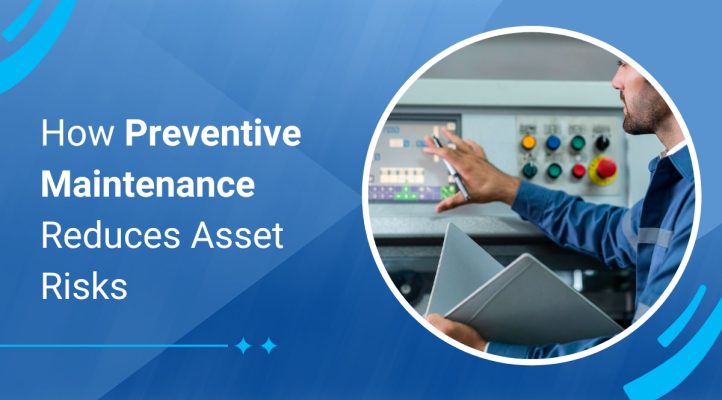
Asset reliability is essential for maintaining seamless operations in industrial and manufacturing settings. Unexpected equipment failures can disrupt production, lead to safety hazards, and incur costly repairs. A well-implemented preventive maintenance strategy minimizes these risks by ensuring assets remain in optimal condition, reducing downtime, and enhancing overall efficiency.
The Importance of Preventive Maintenance
Preventive maintenance is a proactive approach that involves regularly scheduled inspections, servicing, and repairs to prevent unexpected failures. Unlike reactive maintenance, which only addresses issues after they occur, preventive maintenance anticipates problems before they escalate, minimizing downtime and extending asset lifespan.
Key benefits of preventive maintenance include:
- Reduced Downtime: Scheduled maintenance prevents unexpected breakdowns, ensuring consistent production flow.
- Cost Savings: Addressing minor issues early prevents expensive repairs and unplanned shutdowns.
- Enhanced Safety: Well-maintained assets minimize the risk of workplace accidents and regulatory non-compliance.
- Optimized Asset Performance: Regular servicing improves efficiency, reduces energy consumption, and extends equipment longevity.
How Asset Monitoring Enhances Preventive Maintenance
Effective preventive maintenance relies on continuous asset monitoring. Modern technologies enable real-time tracking of asset health. By collecting and analyzing data on equipment performance, businesses can:
- Identify Early Warning Signs: Detect anomalies before they lead to critical failures.
- Schedule Maintenance Efficiently: Use predictive insights to determine the best times for servicing, avoiding unnecessary disruptions.
- Improve Resource Allocation: Allocate maintenance personnel and spare parts more effectively, reducing waste and downtime.
Implementing a Preventive Maintenance Strategy
To maximize the benefits of preventive maintenance and asset monitoring, businesses should follow these best practices:
- Develop a Maintenance Schedule: Establish routine check-ups based on manufacturer recommendations and historical performance data.
- Leverage Technology: Utilize asset monitoring systems to track real-time performance and predict potential issues.
- Train Personnel: Ensure maintenance teams understand equipment requirements and can interpret monitoring data effectively.
- Document and Analyze Data: Keep detailed records of maintenance activities to refine and improve future strategies.
Rhythm Innovations: Empowering Preventive Maintenance
Rhythm Innovations offers a comprehensive platform to streamline preventive maintenance and asset monitoring. Our technology integrates real-time data tracking, predictive analytics, and automated maintenance scheduling to help businesses proactively manage their assets. By leveraging Rhythm Innovations’ platform, organizations can optimize equipment performance, reduce operational risks, and ensure long-term sustainability.
Conclusion
Preventive maintenance is a critical component of risk management in asset-intensive industries. By proactively maintaining equipment and leveraging asset monitoring technologies, businesses can enhance operational efficiency, reduce unexpected failures, and ensure a safer working environment.
Rhythm Innovations provides advanced solutions to help businesses implement effective preventive maintenance and asset monitoring strategies. Contact us today to learn how our technology can safeguard your assets and optimize performance.